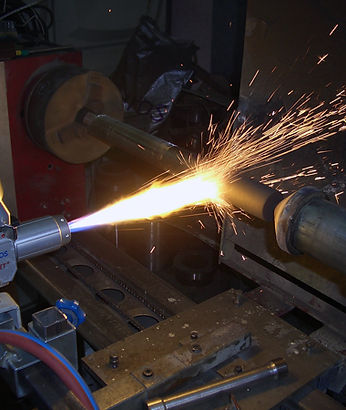




Газопламенное напыление
и наплавка
Термическое напыление (металлическое напыление) — процесс покрытия ( обработка поверхности), где широкий спектр металлов и керамики распыляется на поверхность другого материала.
В данный момент у нас в наличии имеется газопламенное напыление, которое широко используется для обеспечения защиты коррозии черных металлов или изменения их поверхностных свойств для улучшения параметров износостойкости или тепловой проводимости.
Газопламенное напыление предполагает формирование капель (частиц) малого размера
расплавленного металла и перенос их на обрабатываемую поверхность, где они удерживаются,
формируя тем самым непрерывное покрытие.
Процесс создания расплавленных частиц осуществляет мощный источник высокой температуры. После первичного контакта с обрабатываемой поверхностью частицы сглаживаются на ней, застывают и механически закрепляются, с начала, на основании и затем друг на друге, поскольку толщина покрытия увеличивается в процессе обработки.
Так как в расплавленных частицах содержание тепловой энергии по отношению к размеру
распыляемых компонентов мало, то во время процесса на основу передается очень маленькое
количество тепловой энергии. В связи с тем, что повышение температур в распыляемых частицах
минимально, то тепловой деформации не наблюдается. Это является основным преимуществом термического напыления перед способом горячей гальванизации.
Газопламенное напыление — это технология, которая защищает и значительно продлевает срок
службы различного рода оборудования в самых неблагоприятных условиях и в ситуациях, когда
покрытие имеет жизненно важное значение.
Существует огромное разнообразие металлопокрытий, но из всего этого многообразия можно
выделить 2 основные группы:
-
Группа 1 — антикоррозионные и декоративные покрытия;
-
Группа 2 – инженерные покрытия, такие как износостойкие и теплоизолирующие.
Какие же детали подходят для процесса напыления?
Пригодность процесса газопламенного напыления для той или иной области применения можно определить, опираясь на следующие фундаментальные принципы:
-
Напыление не возможно, если поверхность обрабатываемой детали подвержена точечной нагрузке. Например: игольчатые ролики и пазы роликоподшипников, где несущие элементы находятся в непосредственном контакте с напыленным покрытием.
-
Напыление не возможно, если часть поверхности детали или вся поверхность детали подвержена поперечной нагрузке. Например: зубья шестерни, пазы, резьба и т.д. не могут быть восстановлены с помощью напыления
-
Материалу основы не придается дополнительная прочность благодаря напылению. Поэтому очень важно подготовить деталь под напыление таким образом, чтобы она выдерживала механическую нагрузку, которой она будет подвергаться во время процесса обработки. Например: изношенная до состояния, превышающего допустимую норму, необходимую для шлифовки, ось коленчатого вала не может быть восстановлена.
-
Напыление не возможно, если поверхность детали подвергалась процессу упрочнения, такому, как азотирование.
В процессе газопламенного напыления все нанесенные материалы имеют способность, остывая, сжиматься. По причине усадки возникают напряжения внутри обрабатываемой поверхности, могут образовываться трещины, либо происходить отслоение покрытия. Степень усадки поверхности зависит от используемого материала. Выбор наносимого покрытия также зависит от способа последующей обработки поверхности (шлифование, обработка на токарном станке, обработка на фрезерном станке). Вследствие чего, необходимо правильно подходить к выбору того или иного материала под каждый вид работ.
Нанесение металлов напылением
Назначение покрытий:
- улучшение коэффициента трения поверхности;- повышение твердости или пластичности поверхности;- защита от коррозии, эрозии, кавитации;- температуростойкость и окалиностойкость;- исправление деталей, сделанных с ошибками, и восстановление изношенных деталей допервоначального размера. Преимущества:- может быть создан практически любой состав покрытия для толщины покрытия от сотых долей донескольких миллиметров;- при нанесении покрытия основной материал нагревается обычно до температуры 100 – 150 0С, приэтом не наступает изменение структуры и коробления;- покрытие можно наносить на различные материалы вне зависимости от размеров деталей;- тонкозернистое микропористое высококачественное покрытие имеет идеальные предпосылки для слоистых технологий.
Кратко о материалах для напыления и области применения
Цинк (Zn)
Анодная защита на стали и в щелочной среде, воде до 600 0 С, используется при конструировании вобязательном порядке в машиностроении, горном строительстве и кораблестроении, для холодильных установок без опасности коробления. В сравнении с горячим цинкованием нет повреждения металлотравлением. Слои, напылённые металлическим цинком, значительно чище, чем полученные другими способами.
Алюминий (Al) 99,5 – 99,9 %
Наряду с применением для коррозионной защиты алюминий используется и в других областях:покрытия для посуды (хорошая теплопроводность), в пищевой промышленности, при высокихтемпературах воды, кислотной атмосфере, для алитирования, для защиты от возгорания.
Сплав Al – Mg
Стойкий к морской воде, полируемые покрытия с высокой прочностью сцепления, пригодны для пищевой промышленности, изготовления транспортных средств и тепловых приборов и устройств.
Олово – бронза (Sn – Bz)
В первую очередь для подшипников скольжения. Высокая износо- и коррозионная стойкость. Плотнаяструктура напылённого покрытия, высокая чистота поверхности и превосходные антифрикционныесвойства со сталью. Декоративные покрытия.
Медь (Cu)
Электротехника, экранирующие покрытия, покрытия транспортных роликов, бумажных валков, нажимных роликов, клеевых вальцев. Электропроводящие покрытия на непроводниках. Медныеэлектроды для технологии искровой эрозии. Декоративные покрытия.
Латунь (Ms)
Покрытия валов и вальцев вместо массивной латуни. Значительное улучшение сцепления резины состалью.
Подшипниковый материал (Zn-Sb-Cu)
Высококачественный материал на основе цинка, без усадочных и газовых пор, для подшипников свысокими статическими и динамическими нагрузками, отличные смазывающие свойства благодаряобразованию на поверхности плёнки с высокой твёрдостью. Изготовление подшипников напылениемзначительно проще и экономичнее, так как обычно не требуется предварительная механическаяподготовка вкладыша и литьё толстых слоёв. Хорошая теплопроводность.
Олово (Sn)
Коррозионная защита ёмкостей для пищевой промышленности, разбавленных органических солей.Создание сопел напылением негативных моделей. Возможно напыление на дерево или гипс.
Никель (Ni)
Создание подслоя, буферного слоя, коррозионная защита сушильных цилиндров в бумажнойпромышленности. Ванны для двууглекислого натрия или паташа, насосы, химические аппараты.
Монель (Ni-Cu)
Сплав с низкой усадкой и высокой стойкостью к многим видам коррозии, обладает также относительной износостойкостью. Очень хорошо обрабатывается.
445 алюминиевая бронза (Cu-Al-Composite-Pulver)
Для мягких подшипниковых поверхностей с чрезвычайно высокой изностойкостью. Высококачественный термореагирующий материал. Хорошая прочность на острых кромках. Пригодендля тонких и толстых слоёв. Гладкая поверхность. Некоррозионностойкий.
447 Универсальный материал (Mo-Ni-Composite-Pulver)
Средняя твёрдость, вязкие слои с ударной вязкостью, износостойкий, стойкий к эрозии частицами итрению, а также к задирам с твёрдыми и мягкими поверхностями деталей. Очень высокая адгезионная прочность.
13% хромистая сталь
Трудноокисляемая твёрдая сталь с превосходными антифрикционными свойствами, низкимкоэффициентом усадки, поэтому пригодна для толстых слоёв, например, для ремонтаповоротнолопастных турбин гидроэлектростанций. Используется для цилиндров, валов вентиляторов,плунжеров, цапф коленвалов, водяных затворов, навивочных оправок, барабанов волочьиных станов,прессовых насадок, рольгангов и т.д. Используется при высокой нагрузке, обладая твёрдостью 49-52HRC и высокой прочностью сцепления 30-40 kp/cm2. Рекомендуется шлифовать.
17% хромистая сталь
Нержавеющая сталь легированная 0,4% углерода и 1,85% Mo. Покрытие вязко-твёрдое, магнитное.Используется для износостойких слоёв при высоких нагрузках. Обычная твёрдость 40-42 HRC.Рекомендуется шлифовать.
Углеродистая сталь 100 (0,9 С – 99,1 Fe)
Сталь с высоким содержанием углерода с отличной износостойкостью. Твёрдость 55 HRC,обрабатывается шлифованием.
Алюминий – железо – бронза (Al Bz 8 Fe)
При напылении этот материал получает высокую твёрдость и износостойкость. Хорошообрабатывается. Особенно применим для высоконагруженных подшипников, букс, фрикционныхповерхностей, станин, вилок переключения, гидропоршней и т.д. Пригоден для псевдолегирования суглеродистыми и хромистыми сталями.
Молибден (Mo) 99,9%
Благодаря своим выдающимся металлургическим свойствам молибден обладает хорошейспособностью к сцеплению (адгезии). Очень тонкие мелкозернистые слои позволяют напылять толщину покрытия менее 0,05 мм. Можно шлифовать до нуля. Из-за микропористости покрытие имеет очень хорошие антифрикционные свойства, которые могут быть повышены в сочетании с графитом.Напыляемые частицы привариваются к подложке, обеспечивая высокую адгезию, что идеальноподходит для исправления брака, ремонта, снижения допусков. Не применяется для азотированных ихромированных поверхностей, для деталей из меди или медесодержащих (более 20%).
Нихром (Ni-Cr 80/20)
Специальное применение в качестве подслоя и кислородного барьера для окисной керамики в несодержащей серу атмосфере. Хорошо пригоден для защиты от окисления для деталей, работающих вперегретом паре. Сопротивление к окислению при температурах до 1200 0С. Также наносится надетали, которые непосредственно после нанесения покрытия должны быть хорошо обработанымеханически, например, футеровочные работы. Хорошая стойкость к истиранию. Высокое качествоповерхности.
Хромо-никелевая сталь (1.4571)
Катодный немагнитный защитный слой для паровых и сушильнокрасильных вальцев, вальцев дляотвердения в производстве резины, сушильных цилиндров бумажных машин, для облицовки ванн иёмкостей, трубные доски теплообменников. В соединении с пластмассой получается твёрдыйизносостойкий с хорошей эластичностью слой, противостоящий коррозии и истиранию (R-H-K –технологии).
Никель-алюминий (Ni – Al 95/5)
Отличный 1054 подслой с высокой адгезией (65 – 75 kp/cm2). Частичная свариваемость с подложкойблагодаря экзотермической реакции. Пластичный промежуточный слой. Может работать при высокихтемпературах.
Г
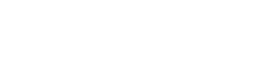
"СВАРНОЙ"
Профессиональные сварочные услуги
8-908-174-14-14 8-903-464-32-33